With the continued development and improvement of electric vehicle battery technology, it’s easy to imagine the future of transportation: a world where everything from personal cars and SUVs to the trucking industry runs on batteries. Carbon emissions will be reduced dramatically. But that’s just the start. Old batteries from electric vehicles (EVs), when reused, promise to change the world in even more profound ways by bringing small, off-grid power to remote regions of the world where healthcare, educational and economic development hinges on access to affordable, renewable energy.
While the groundwork for this future is already being laid, battery manufacturers still face substantial challenges, from reducing the high cost of electric vehicle batteries so they’re competitive with internal-combustion engine vehicles, to building batteries with reuse and recycling in mind so that when they’re no longer viable for electric vehicles, they’re valuable for other worthy purposes.
So what does it take to make a battery-powered future a reality? The answer depends not only on getting buy-in from consumers, policymakers, and utilities but also on forging the right partnerships and making the right investments.
LEADING THE CHARGE
There’s a palpable feeling of excitement around the potential of electric vehicles, particularly with regard to environmental impact. More businesses are making sustainability a priority, and studies are showing that eco-conscious practices can translate to increased sales. The EV space is no different. In 2018, global electric car sales exceeded the 2 million mark (2.1 million), after crossing the 1 million mark in 2017, rising 65%. But in 2019, sales increased only 9% to 2.3 million, impacted by an overall decline in global automobile sales. Nonetheless, a tenfold increase in the demand for EVs is expected by 2030. Nearly every region of the world has renewed its EV incentives, and every major OEM is on track to electrify its vehicle fleet. The world is doubling down on electricity.
Still, the electric vehicle industry has a price comparison problem. While the cost of EV batteries are projected to decline in the years leading up to 2030, battery expense remains one of the major barriers to overall price parity with gasoline-powered vehicles, accounting for more than a third of the cost of an electric vehicle.
One potential solution is employing highly accurate and safe battery management systems (BMS), which help automakers and parts manufacturers bridge the gap between today’s high-cost batteries and tomorrow’s more affordable ones.
“There are several major issues from a consumer perspective,” says Patrick Morgan. “Larger batteries enable longer ranges. The problem is that they add cost and weight. We’re solving that problem by making extremely efficient and accurate electronics for battery management systems that enable getting the most usable energy out of any given battery pack.”
That efficiency is even more critical for industries like trucking, which are beginning to invest heavily in electrification. According to a McKinsey study, up to 20% of medium-duty trucks could be EVs by 2030—if batteries can keep up with demand. “EVs may require additional downtime for charging that can adversely impact business performance because the vehicles are placed in a non-revenue status longer than gas-powered vehicles,” says Susan Shaheen, co-director of the Transportation Sustainability Research Center at the University of California, Berkeley.
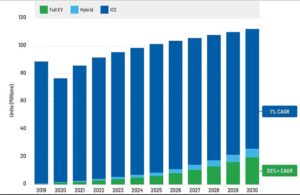
EFFICIENCY BEGINS WITH THE FINISHING STAGE
Recent innovations in electric vehicle battery technology and battery manufacturing and management could be a game-changer in both commercial and consumer contexts. The battery production and finishing stage – battery formation and test – is critical to ensuring efficiency down the line. Battery formation is all about ensuring that the cells are manufactured and created for maximum capacity and maximum reliability for the duration of their life cycle. And for battery manufacturers and instrumentation providers, increasing the scale and efficiency of EV production is the key to capitalizing on the opportunity in the electric vehicle market.
“We sell products that touch batteries at every stage of their lifetime, from formation through operation, and into second life. During formation, our products control precision equipment which grows the cells. This stage of the birth of the battery cell is critical to determining is usable lifetime.” Morgan explains.
BETTER WORKING CONDITIONS FOR BATTERIES
Unlike a single energy storage element, such as a fuel tank, an EV battery pack consists of hundreds or thousands of individual battery cells working together. As power flows into or out of the battery pack, the cells must be precisely managed with guaranteed accuracy to ensure maximum usable battery capacity over the lifetime of the vehicle even in the harshest conditions including extreme temperatures and environments with magnetic and electric noise. On top of that, to ensure safety, electronics must be carefully designed from the beginning to fully comply with all stringent safety standards worldwide, which are in constant evolution around the world. These standards go far beyond just ASIL-D compliance; they require innovative battery functional architectures to be developed.
From there, Analog Devices’ lithium-ion battery management systems for electric vehicles constantly measure the voltage of each cell, which benefits battery range and performance while guaranteeing maximum safety. Highly accurate state of charge measurements give automakers and parts manufacturers the ability to safely maximize output. According to Morgan, “Our products deliver the world’s best accuracy guaranteed for the lifetime of the vehicle, which enables fast, safe charging and discharging of the battery to the fullest extent, and provides maximum vehicle range per charge.”
A BETTER BATTERY
Improving electric battery range and performance is crucial to full adoption of electric vehicles. Already, smarter, moreaccurate battery management systems are helping automakers and parts manufacturers get more mileage out of electric batteries.
MILEAGE INCREASE IN EV BATTERIES
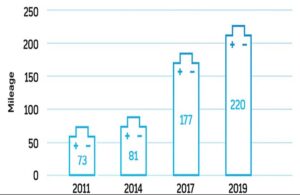
As BMS continues to maximize performance, electric batteries will be better able to support both extended EV driving ranges and autonomous vehicles’ sensors.
UNHARNESSING SYSTEM COMPLEXITY
New, wireless battery management systems are bringing disruptive change to the industry. Built up existing components of the wired BMS, the wireless battery management system (WBMS) recently developed by Analog Devices, eliminates the need for the wire harness that connects the battery cells together, which saves engineering design and development costs, as well as the associated mechanical challenges and complexity of the wire harness. It also allows the battery pack design to become highly modular and scalable so it can be reused across multiple car designs. Also, because each battery module is wireless, data can be collected and stored from the time the cell is formed through storage, assembly, and use within the vehicle, enabling state-of-health calculations that can set a residual value for the battery pack. This reduces the cost of a battery and enables a more efficient second use (or a second life), such as in storage, recycling, or other applications, reducing the overall cost to manufacturer and vehicle owner and limiting environmental impact.
A VEHICLE FOR CHANGE: BATTERY SECOND LIFE
The broader adoption of EVs will have a substantial environmental impact. According to Analog Devices, in 2019, vehicles equipped with the company’s BMS technology saved approximately 75 million tons of carbon dioxide per year—a carbon reduction capability equivalent to 80 million acres of mature forest—by virtue of operating without the need for an internal-combustion engine while leveraging ultra-precise battery performance measurement.
But there’s more to the electric vehicle battery technology story: battery second life. Batteries worn down from EV use are not worn out, if the battery cells were well managed over their life. Breaking down EV batteries for reuse in energy storage solutions can be a key factor in delivering electricity to off-grid communities. Consider that 940 million people (13% of the world’s population) don’t have access to electricity, and a further 3 billion people (40% of the world’s population) don’t have access to clean cooking fuel, and you begin to envision the need for micro and off-grid power solutions.
The life-changing domino effects that access to affordable electricity will bring are many. Eliminating the need for unsafe cooking fuels improves indoor air quality, and therefore health. Electricity can power lighting to allow children to study after dark. Equipment to supply clean water and sanitize wastewater can be powered. And digital communications via internet access can be enabled. In these ways, battery second life has the potential to spark economic development gains once thought unattainable.
This makes the precision Analog Devices brings to battery management systems an even more important consideration for vehicle manufacturers, while second life application owners, such as energy storage system manufacturers, will benefit greatly from Analog Devices’ wireless technology. Not only does the technology support OEMs, it also can help create an entirely new industry and business models around battery recycling. “We are just at the beginning of seeing the benefits that wireless will bring into the vehicle supply chain.” Morgan explains.
CONVENTIONAL ENGINE WISDOM
Twenty years ago marked Analog Devices first introduction of precision power and other measurement solutions to the automotive market. It’s not lost on Vincent Roche, president and chief executive officer, that their decades-long experience building functionality in conventional internal combustion vehicles plays a major role in their successful development of electric vehicle battery technology. “We’re combining our silicon solutions with increasingly sophisticated mathematics to be able to make sense of the real world, including battery management systems where transformative change is increasing by orders of magnitude every few years,” Roche says.